1. Avant-propos
Le développement du système IRIS
- En 1979, Shell Development Company, Westhollow Research Center, Houston, Texas, a développé et construit un système à ultrasons pour inspecter les tubes des échangeurs de chaleur.
- B.I.X. (America), Inc., qui deviendra plus tard Pan American Industries, a acheté l’appareil de Shell pour l’utiliser et le développer. Le nom, IRIS (système d’inspection rotatif interne), qu’ils ont donné à l’appareil est désormais le nom générique de tout appareil soumis au brevet de Shell.
- Au fil des ans, Pan American est devenu un spécialiste des inspections de tubes. Ils étaient conscients des problèmes et des limites du système d’origine. Pan American a ensuite utilisé ses connaissances acquises grâce à ses services pour la recherche et le développement afin de construire un système IRIS plus efficace.
- Sous la licence de Shell, Pan American a développé une version plus compacte du système IRIS et a augmenté ses options d’inspection. Le modèle actuel, série IV, est un système très fiable et convivial.
- En 1997, Pan American Industries a développé un système IRIS numérique. Le nouveau système permet de stocker toutes les mesures dans l’ordinateur et de visualiser les résultats des mesures à l’aide d’un C-scan.
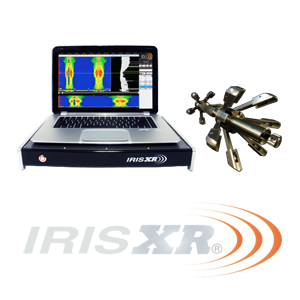
2. Introduction
Général
- Les échangeurs de chaleur et les chaudières à vapeur contiennent de nombreux tubes, chacun étant à son tour soumis à un certain degré de corrosion.
- L’épaisseur de la paroi, là où le tube est le plus mince, détermine s’il convient à une utilisation ultérieure. Si l’épaisseur de la paroi a diminué pour permettre au tube de fuir ou de se fissurer en raison de la pression interne, ou s’il peut être prévu que l’épaisseur de la paroi sera réduite lors de la prochaine inspection programmée, le tube n’est plus adapté à la production. Après tout, un arrêt imprévu dû à la défaillance d’un échangeur de chaleur ou d’une chaudière à vapeur entraîne un coût supplémentaire énorme.
- Bien que la perte générale d’épaisseur de paroi du tube se réfère à la totalité des dommages dus à la corrosion, cela seul n’est pas un facteur fiable pour déterminer l’état du tube. Quelques petites fosses où la paroi est très mince déterminent que le tube ne convient pas pour une utilisation ultérieure, même lorsqu’il y a généralement peu de corrosion. Pour trouver de telles piqûres et mesurer l’épaisseur de paroi, vous avez besoin d’un appareil qui peut mesurer l’épaisseur de paroi sur toute la surface et ce avec une bonne résolution.
- IVT Inspections NV , dispose d’un tel dispositif, à savoir le système IRIS. Après dix ans d’utilisation intensive, le système est devenu un outil d’inspection convivial, qui est maintenant utilisé dans de nombreuses entreprises.
- L’intention initiale du système était de mesurer l’épaisseur de la paroi des tubes d’échangeurs de chaleur refroidis par air (tubes à airfin). IRIS est actuellement utilisé pour la recherche préventive dans de nombreux types différents d’échangeurs de chaleur et de chaudières à vapeur, dans les centrales électriques et nucléaires, les sociétés pétrochimiques et chimiques, les installations offshore, l’industrie maritime et alimentaire, etc…
IRIS utilise la méthode conventionnelle de l’écho d’impulsion pour mesurer l’épaisseur de la paroi, mais utilise une nouvelle méthode pour afficher les résultats de mesure. Toutes les mesures effectuées lors d’un balayage de la circonférence du tube sont imagées sur un écran d’ordinateur. L’image est une coupe transversale rectiligne stationnaire du contour du tube.
- Cette nouvelle façon de présenter a permis de mesurer l’épaisseur de paroi de tubes corrodés jusqu’à une épaisseur minimale de paroi de 0,5 mm. IRIS peut mesurer l’épaisseur de paroi restante, que la perte de métal soit interne ou externe, qu’il s’agisse d’une diminution lisse de l’épaisseur de la paroi ou d’une piqûre locale.
3. Principe de fonctionnement du système IRIS
Principe
- Le fonctionnement d’IRIS est basé sur la technique ultrasonore d’écho d’impulsion pour mesurer les épaisseurs de paroi. Les caractéristiques essentielles de cette méthode sont illustrées à la figure 1a.
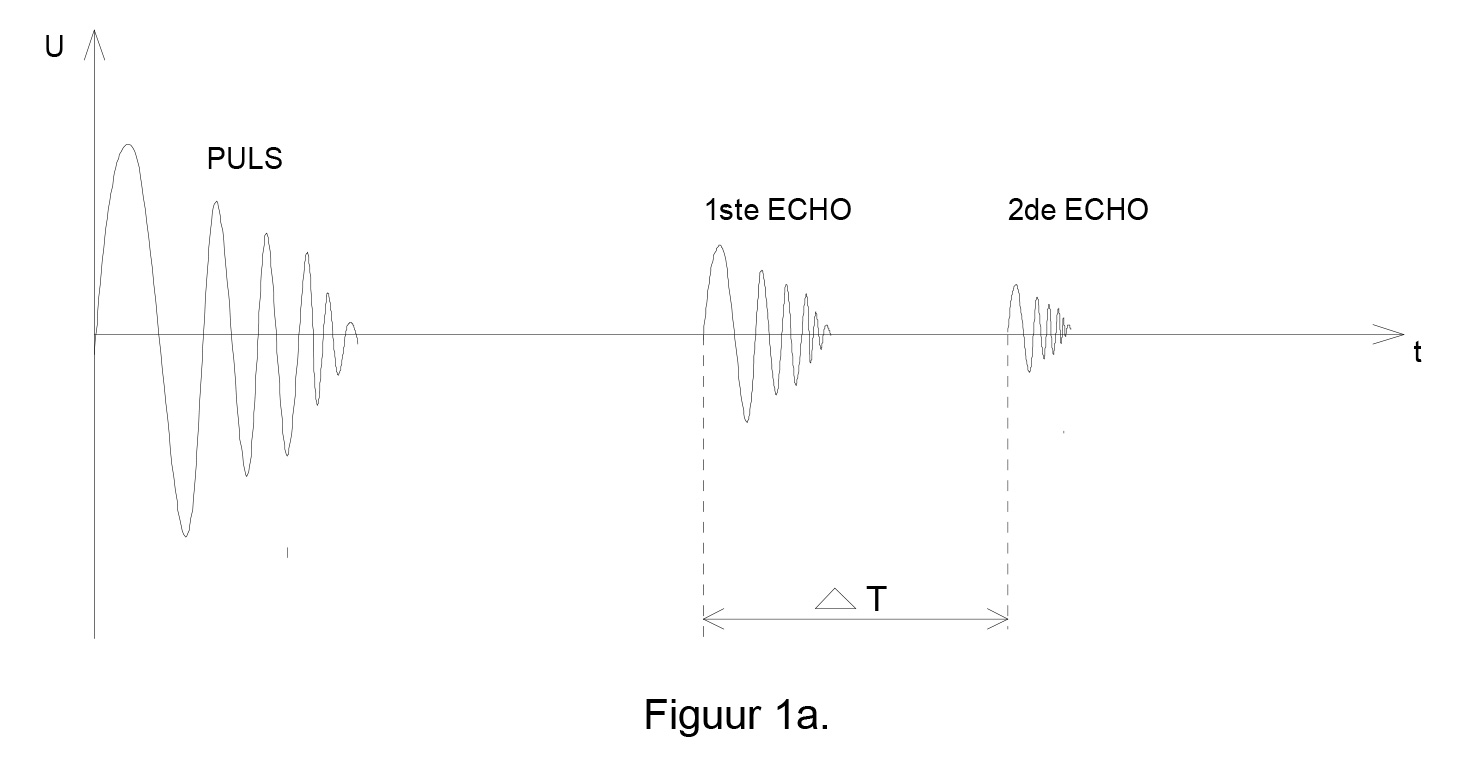
- Un convertisseur convertit une impulsion électrique en une vibration sonore ultrasonique. L’efficacité du transfert d’énergie entre un liquide et un solide étant plus élevée qu’entre un gaz et un solide, IRIS utilise un liquide, à savoir de l’eau, pour conduire les vagues.
- L’impulsion ultrasonore passe à travers l’eau jusqu’à la paroi du tube. Là, la majeure partie de l’énergie de l’impulsion est renvoyée au convertisseur. Une petite partie, environ un dixième, se propage dans la paroi du tube vers la paroi extérieure, où à son tour la deuxième réflexion se produit. Une petite partie de cette deuxième réflexion, environ un dixième, traverse à nouveau le tube à travers l’eau jusqu’au convertisseur.
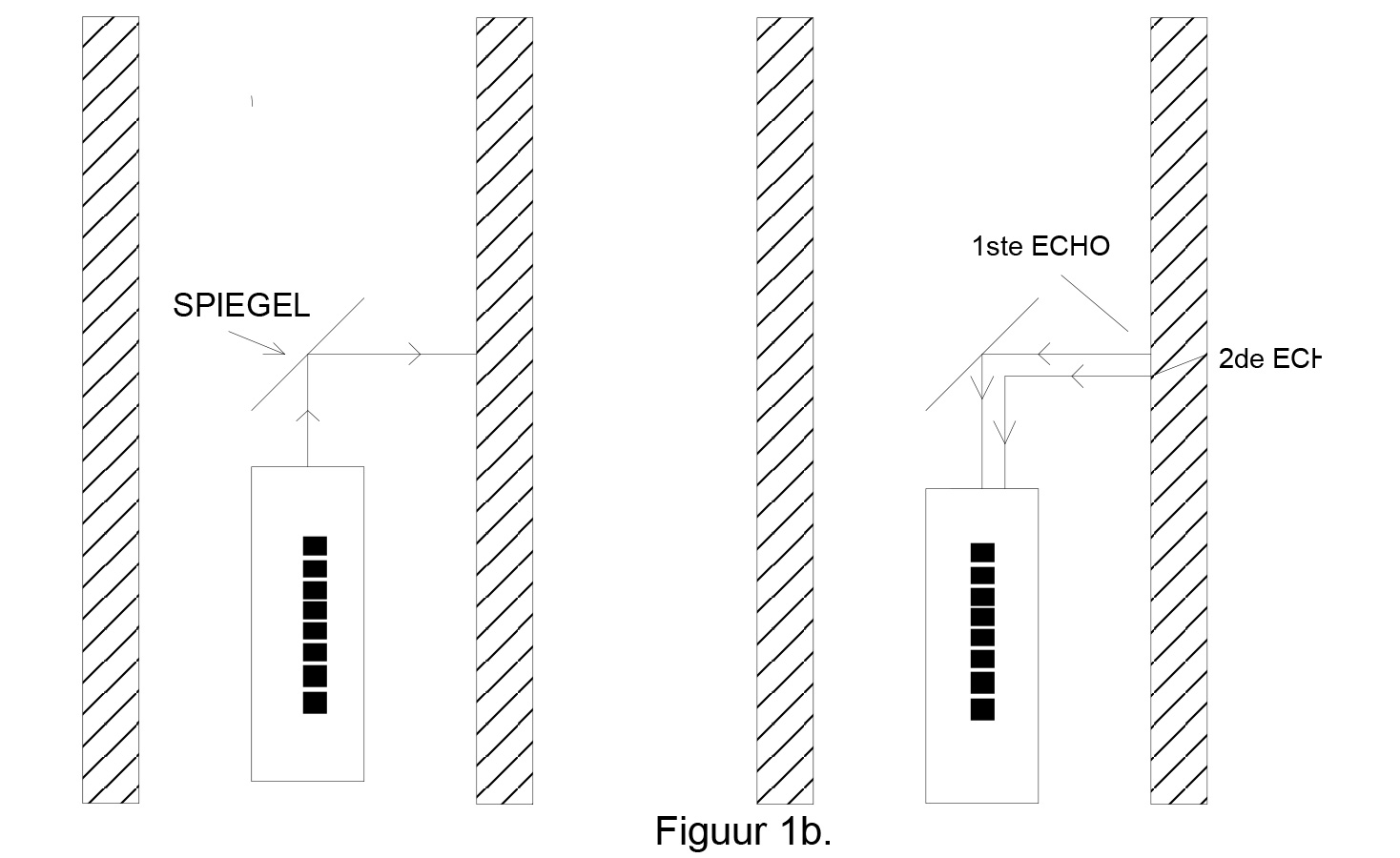
- Les deux échos suivent le même chemin que l’impulsion d’origine. Dans le convertisseur, ils génèrent des impulsions électriques, séparées par le temps, pour se propager à travers toute la paroi du tube. Comme ce temps est proportionnel à l’épaisseur de la paroi, il peut être calculé en mesurant la différence de temps entre les échos de la paroi intérieure et de la paroi extérieure. Cela se fait par voie électronique.
4. La sonde à ultrasons
La sonde
- La manière dont la méthode de l’écho d’impulsion est utilisée pour examiner les tubes de l’échangeur de chaleur et de la chaudière à vapeur est illustrée à la figure 2. Le transducteur à ultrasons est monté dans la sonde, qui est centrée dans un tube.
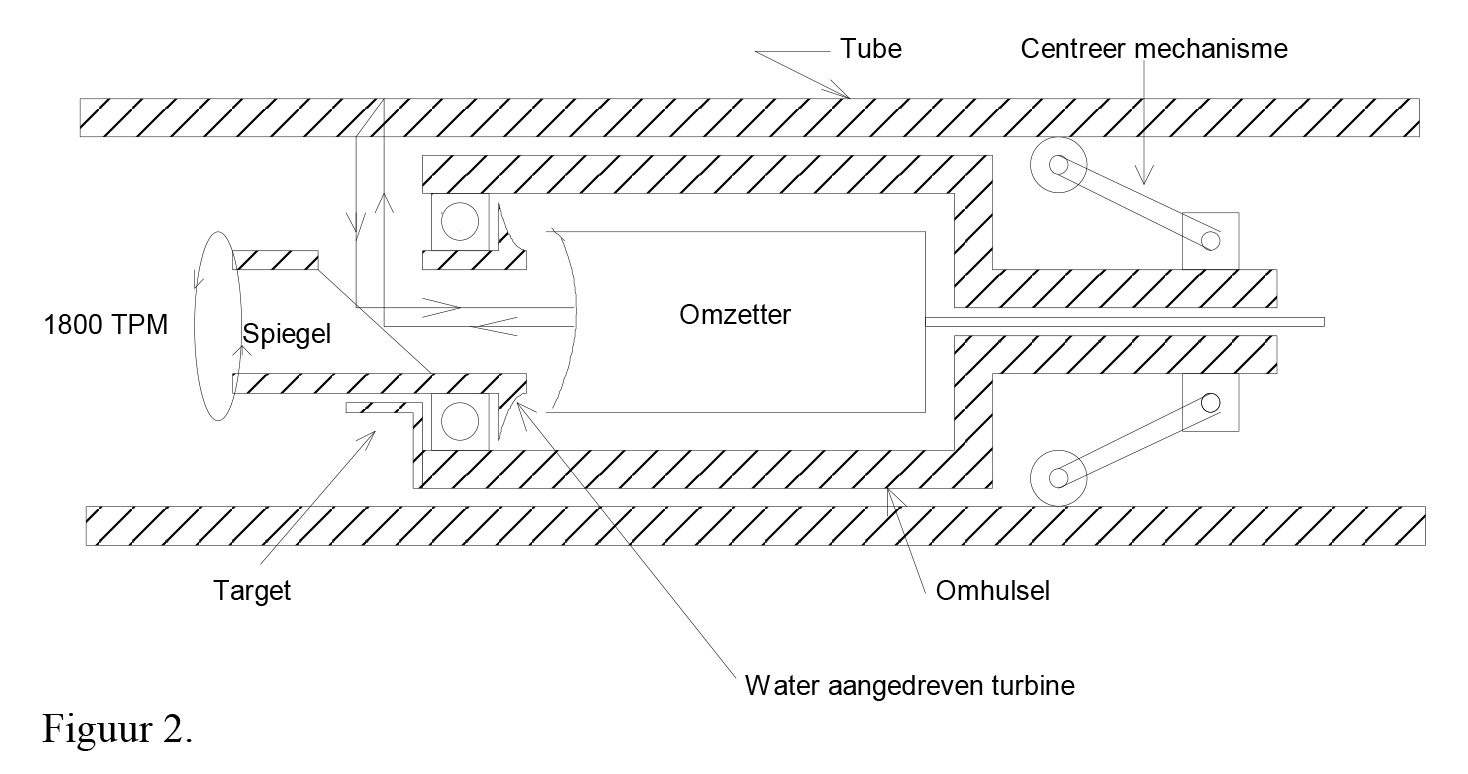
- Les impulsions ultrasonores sont émises parallèlement à l’axe de la sonde. Ces impulsions sont réfléchies sur un miroir tourné à 45 ° de façon à être perpendiculaires à la paroi du tube (Fig. 1b).
- Le miroir est monté sur une turbine hydraulique tournant sur un axe parallèle à l’axe de la sonde. Au fur et à mesure que le miroir tourne, les impulsions ultrasonores successives balayent la circonférence de la paroi du tube, de sorte que toute la circonférence est balayée pendant un tour du miroir.
- Avec une fréquence de répétition des impulsions de 10 kHz et une vitesse de rotation du miroir de 1800 tr / min, toute la paroi est balayée et aucune partie de la circonférence de la paroi du tube ne sera manquée.
5. L'affichage électronique
Affichage
- Ce qui rend ce système si unique, c’est la façon dont les mesures d’épaisseur de paroi par écho d’impulsion sont visualisées.
- Le temps entre la réflexion de la paroi intérieure et extérieure et le temps proportionnel à la distance entre l’axe du miroir et la paroi du tube sont mesurés. Ces mesures sont traitées électroniquement. Toutes les mesures prises pendant une rotation du miroir sont affichées sur un écran d’ordinateur, qui montre une image stationnaire et linéaire de la section transversale du mur.
- La figure 3 montre comment l’image est générée.
- En haut de la figure se trouve le diagramme temporel de l’impulsion émise et des échos réfléchis par la cible (déclenchement), la paroi intérieure et extérieure.
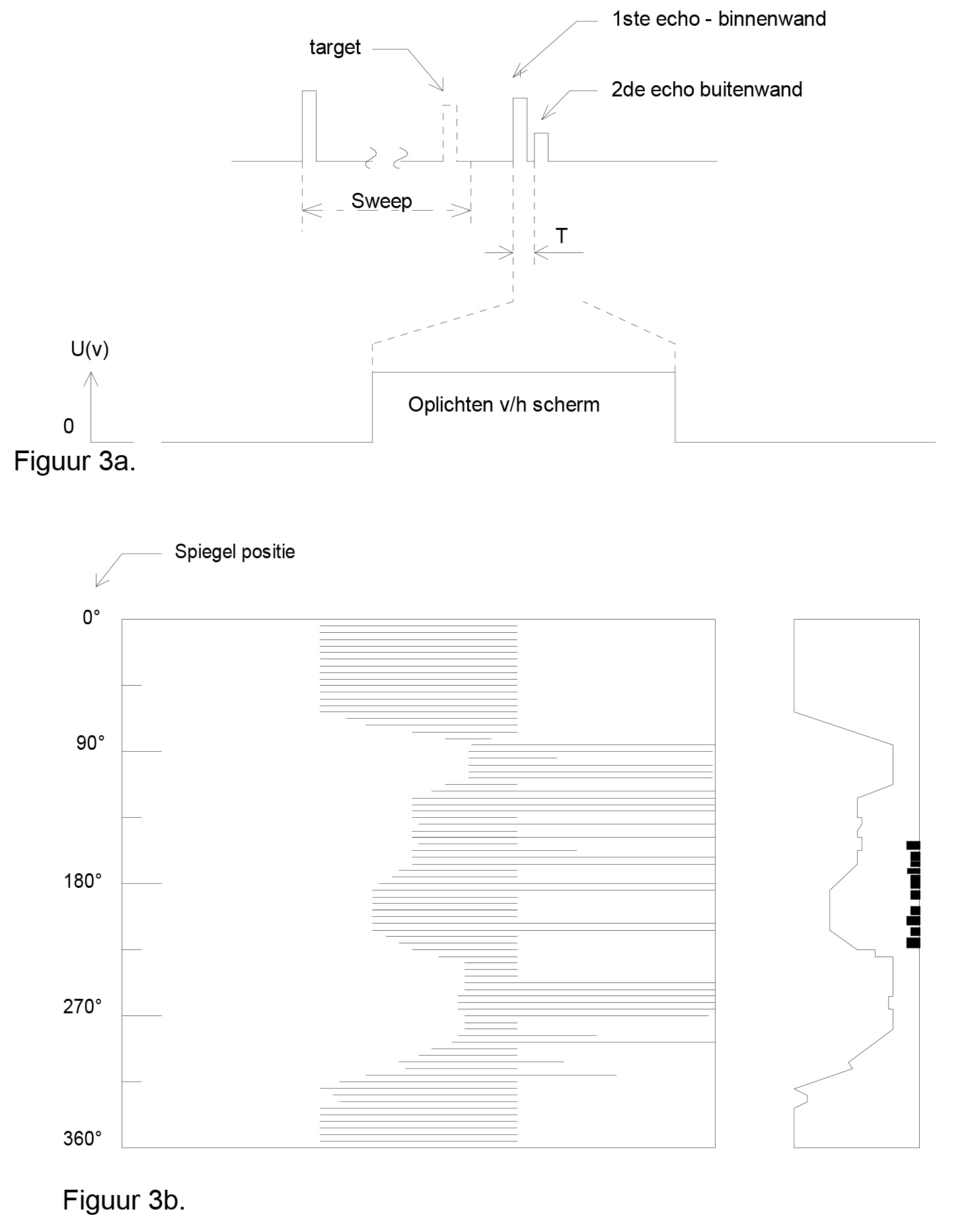
6. Structure de l'image
Interprétation de l'image
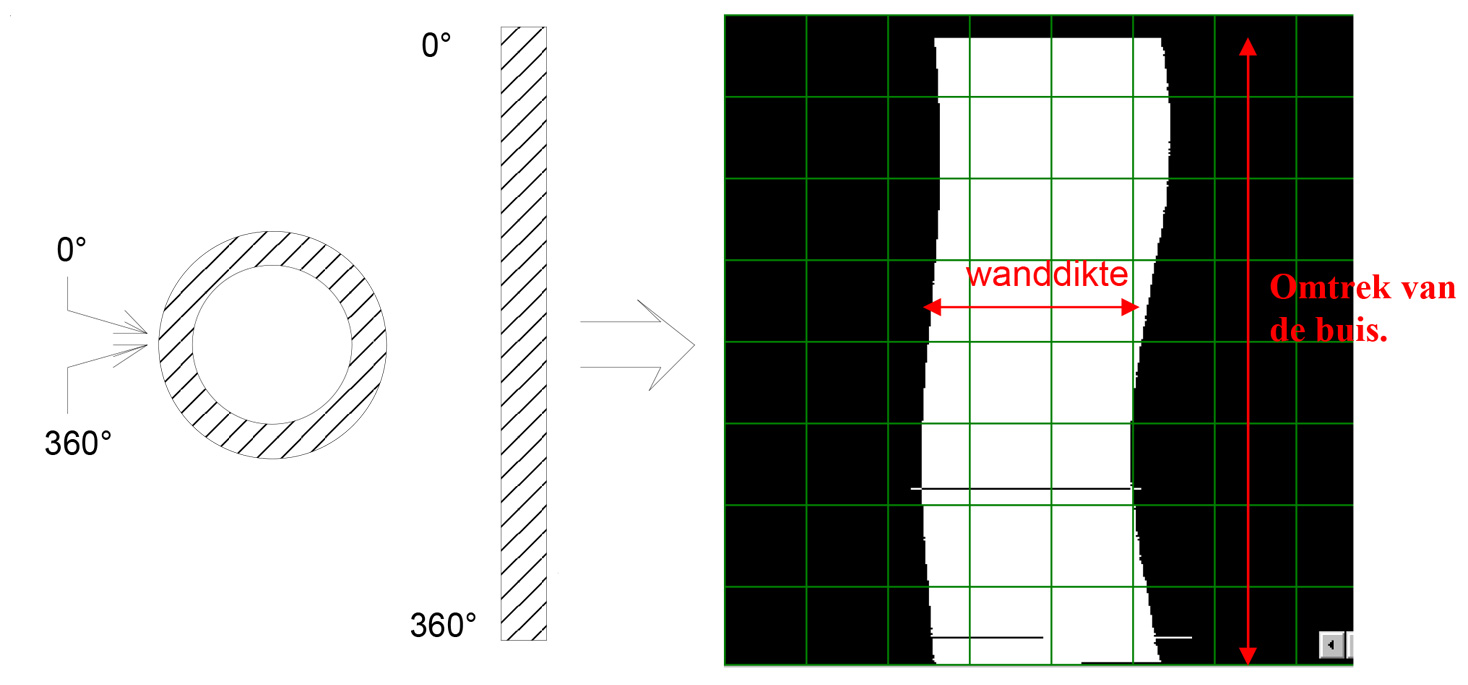
Fonctionnement général et principes du système numérique IRIS:
- Comme suggéré ci-dessus, la hauteur de l’image correspond à la circonférence du tube.
- La largeur du rectangle blanc représente l’épaisseur de paroi du tuyau.
- Le côté gauche est la paroi intérieure du tube, le côté droit du rectangle blanc est la paroi extérieure du tube.
7. Exemples
Général
- Un tube non corrodé crée un motif rectangulaire vertical sur l’écran de l’ordinateur.
- La largeur de ce motif est égale à une mesure de l’épaisseur de la paroi, et la hauteur du motif correspond à la circonférence complète du tube.
Défauts internes
- La corrosion interieur dans un tuyau est facilement identifiée comme des défauts sur le côté gauche de la cartouche rectangulaire.
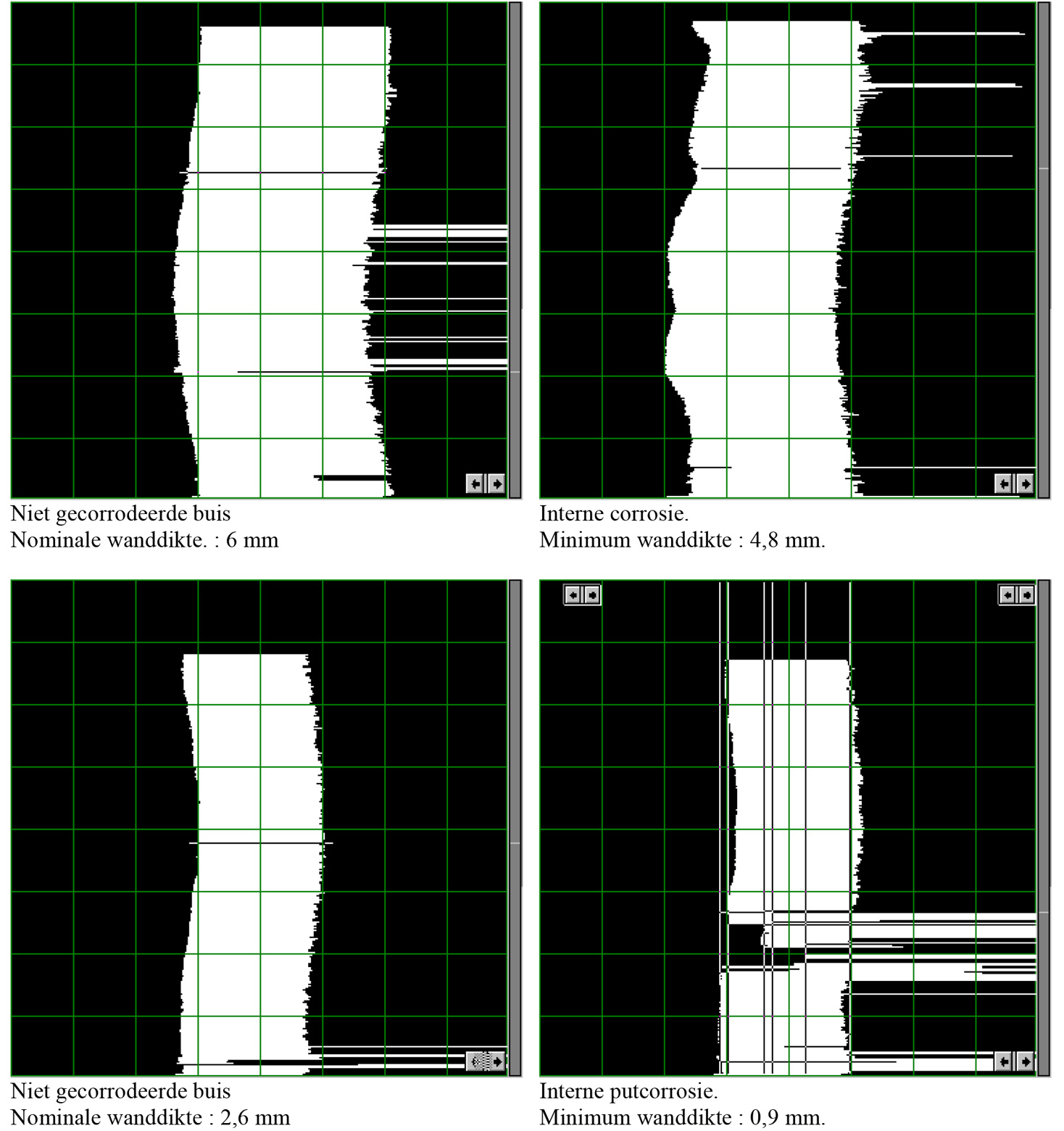
Défauts externes
- La corrosion externe dans un tuyau est facilement identifiée comme des défauts sur le côté droit de la cartouche rectangulaire.
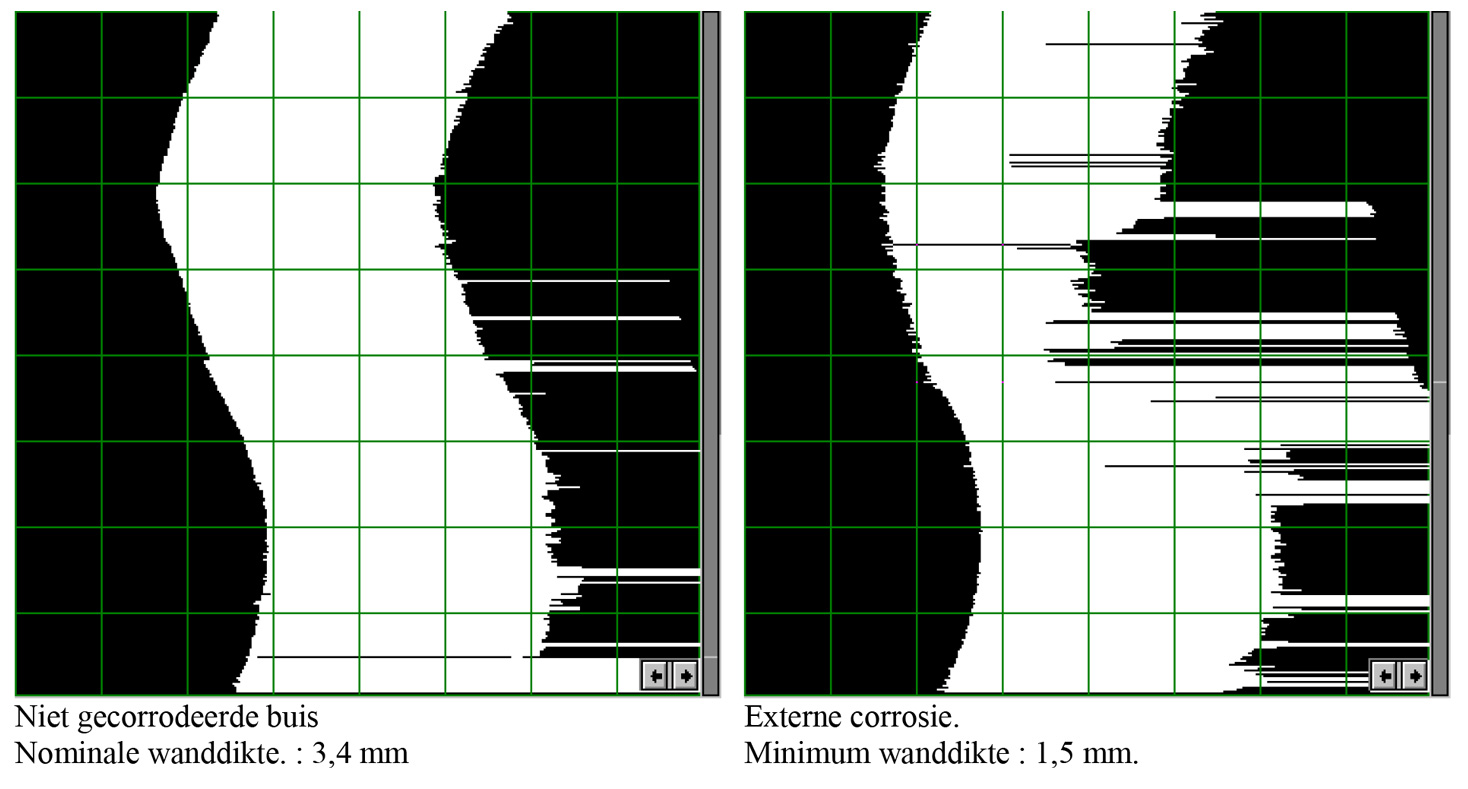
C-scan
- Avec le nouveau système numérique IRIS, il est possible de visualiser la longueur du tube au moyen d’un C-scan.
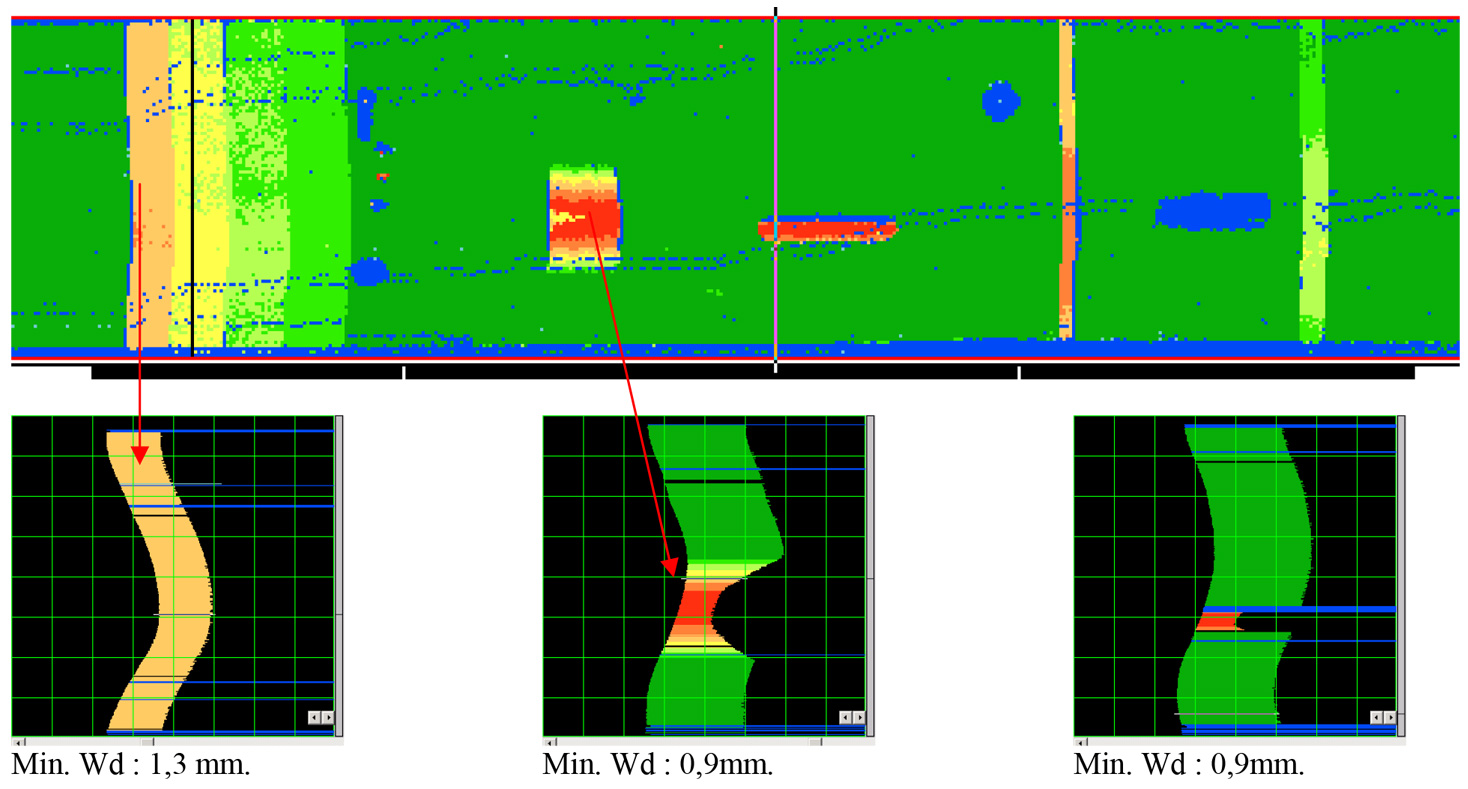
8. Procédure d'inspection
- L’échangeur de chaleur et les tubes de la chaudière DOIVENT être nettoyés avant de pouvoir être inspectés. Il ne devrait plus y avoir de copeaux ou autres saletés dans les tubes. Un nettoyage haute pression est recommandé (min. 1000 bar). Dans des cas exceptionnels, un nettoyage à sec est recommandé.
- Avant que l’inspection ne puisse commencer, toutes les données du faisceau doivent être connues pour l’étalonnage et les rapports. Disposition des plaques, dimensions des tubes, matériau des tubes (vitesse du son).
- Dans un tube relativement bon, le motif à l’écran ne changera pas beaucoup et la sonde peut être poussée à vitesse maximale. Si le tube est fortement corrodé, la vitesse d’inspection doit être réduite afin d’interpréter avec succès le motif en constante évolution sur l’écran.
- La vitesse d’inspection maximale est de 2,6 m par minute si nous voulons détecter des piqûres de corrosion d’un diamètre de 1,5 mm. Des vitesses plus élevées sont possibles si aucune piqûre n’est attendue.
9. Spécifications
- Le plus petit puits que nous pouvons détecter a un diamètre de 1,5 mm pour un tube d’un diamètre extérieur de 2,5 cm.
Modèle: Digital IRIS
Alimentation: 110 V, 220 V a.c.
Consommation: Max. 120W
Approvisionnement en eau: Min. 3 bars d’eau pure sans bulles d’air
Plage de température: 2 °C à 48 °C
Diamètres possibles: 9 mm ID à 100 mm
Pièces centrales: taille 1:17 mm à 26 mm ID, taille 2:23 mm à 43 mm ID, taille 3: 34 mm à 76 mm OD
Diamètres de sonde: taille 1: 12 mm de diamètre extérieur, taille 2: 17 mm de diamètre extérieur
Convertisseurs: 10 MHz, 15 MHz
Longueur des sondes: 15m / 30m
10. Détection de limite
Général
- Plusieurs facteurs déterminent la limite de détection dans les tuyaux de diamètre supérieur à 1 ½ ”(38,1 mm de diamètre extérieur) pour détecter les puits internes ou externes de Ø1,5 mm.
La taille du point AF
- Les transducteurs (transducteurs à ultrasons) ont une distance de focalisation de 45,72 mm. Cela signifie que la taille du point AF est de 1,5 mm à une distance de 45,72 mm du transducteur.
- Pour les tubes de plus gros diamètres, tels que les tubes de 3”, le point focal est augmenté par la divergence du faisceau ultrasonore. Un facteur supplémentaire est l’épaisseur du matériau. Le faisceau ultrasonique diverge plus dans la paroi du tuyau que dans l’eau. Pour déterminer la distance de mise au point, la formule suivante s’applique: « + 4 x épaisseur de paroi ».
- Exemple: si l’épaisseur de paroi du tuyau est de 3,2 mm, la distance de mise au point sera augmentée de 12,8 mm.
- Conclusion: En conséquence, le point focal devient encore plus grand, c’est-à-dire que le diamètre du faisceau ultrasonore augmente.
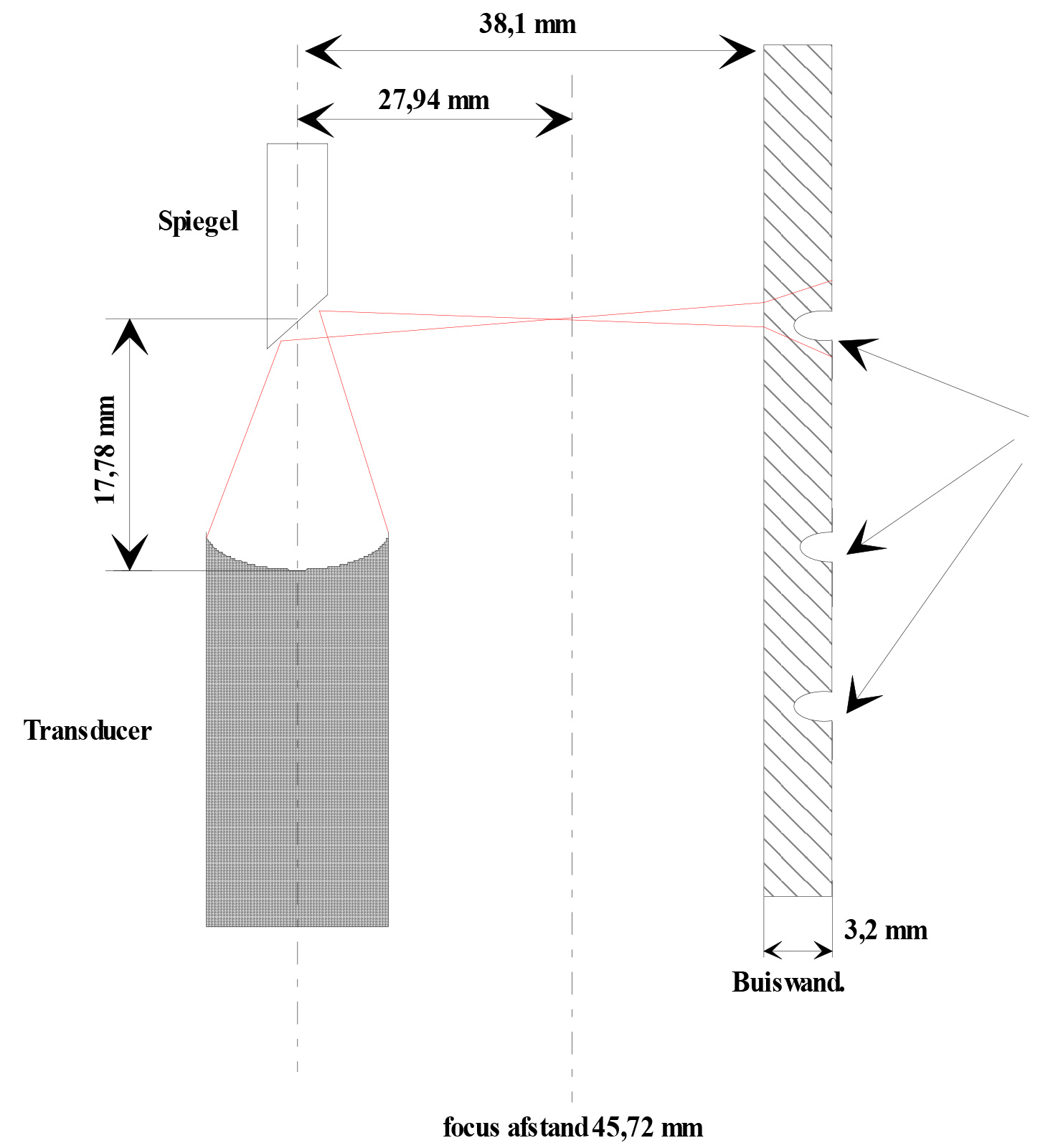
- Pour cette raison, les petits défauts ne peuvent pas être détectés car ils sont occultés par le faisceau ultrasonore.
- Remarque: Les fabricants des transducteurs à ultrasons sont limités à rendre la distance de mise au point supérieure à 45,72 mm.
- Dans certaines circonstances, l’échographie peut toujours ramasser le bord du défaut. Voir figure ci-dessous.
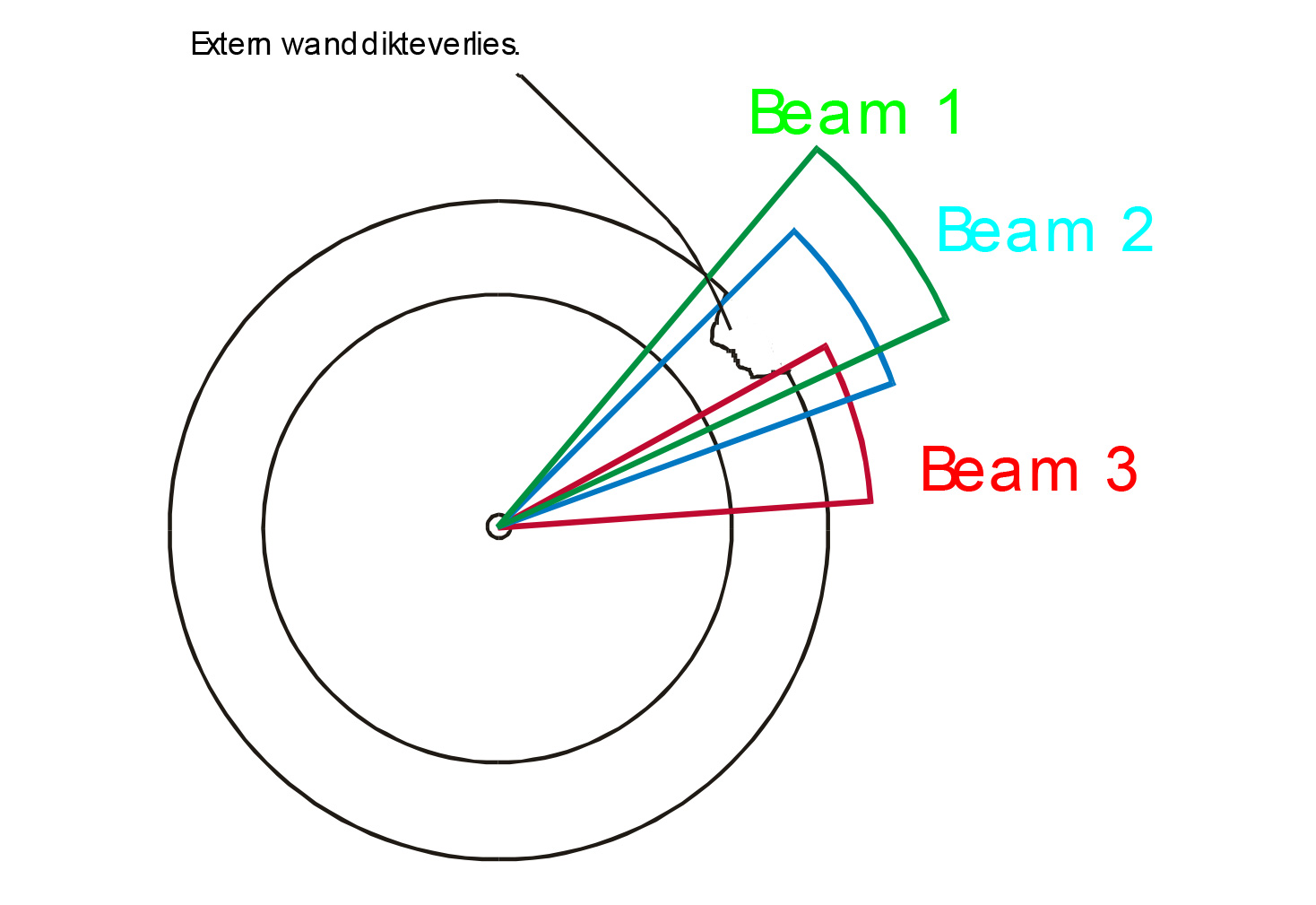
- A) Faisceau 1: la perte d’épaisseur de paroi externe est complètement éclipsée par l’impulsion ultrasonore et n’est pas détectée.
- B) Faisceau 2: Le bord du puits externe est juste détecté par l’impulsion.
- C) Faisceau 3: Le bord du puits externe est juste détecté par l’impulsion.
- En B) et C) aucune perte d’épaisseur de paroi ne peut être observée. Dans certains cas, on ne peut que se référer à une suspicion de perte d’épaisseur de paroi externe car dans ce cas, une petite perte de signal se produit.
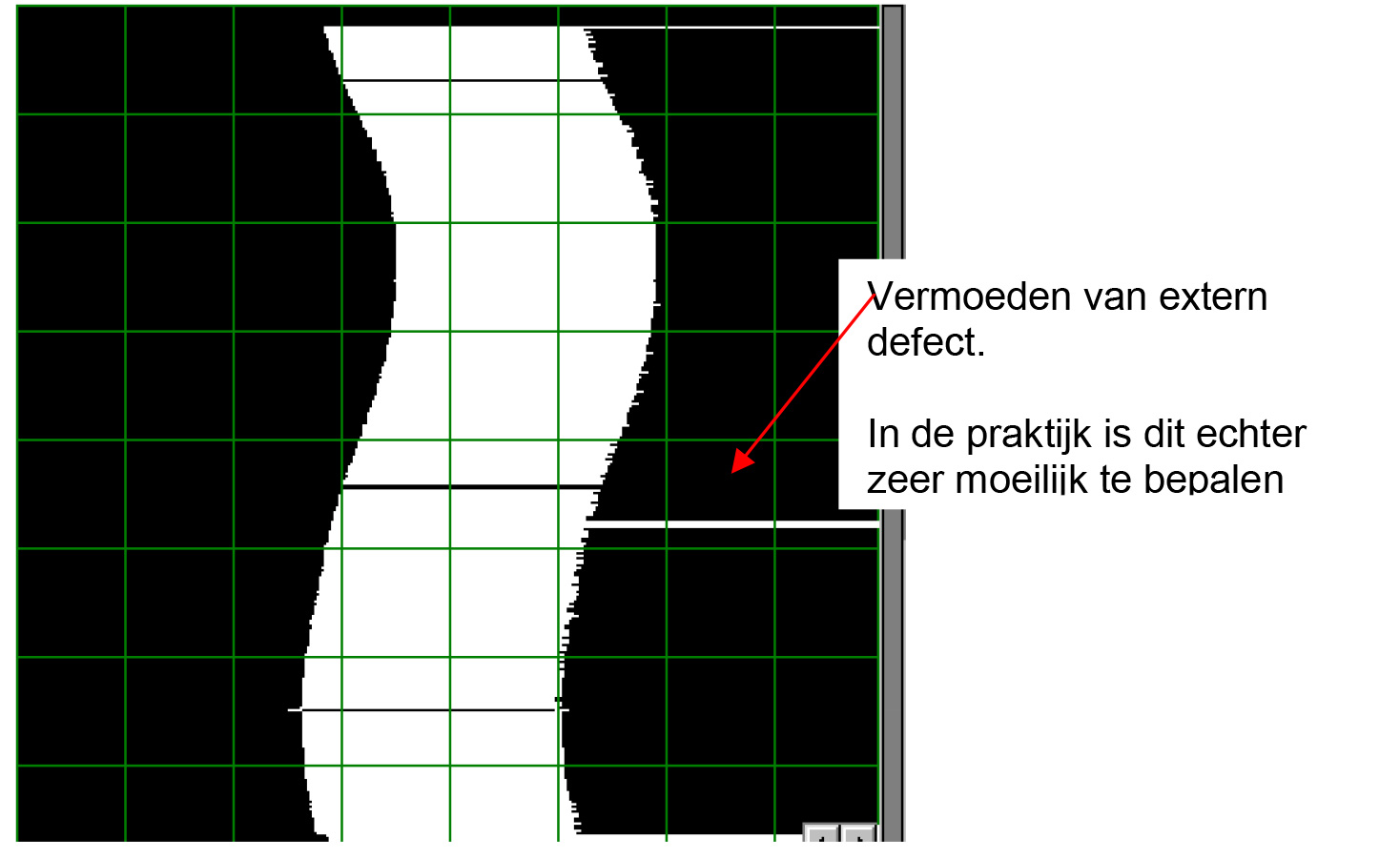
La hauteur de l'écran
- Construction de l’écran.
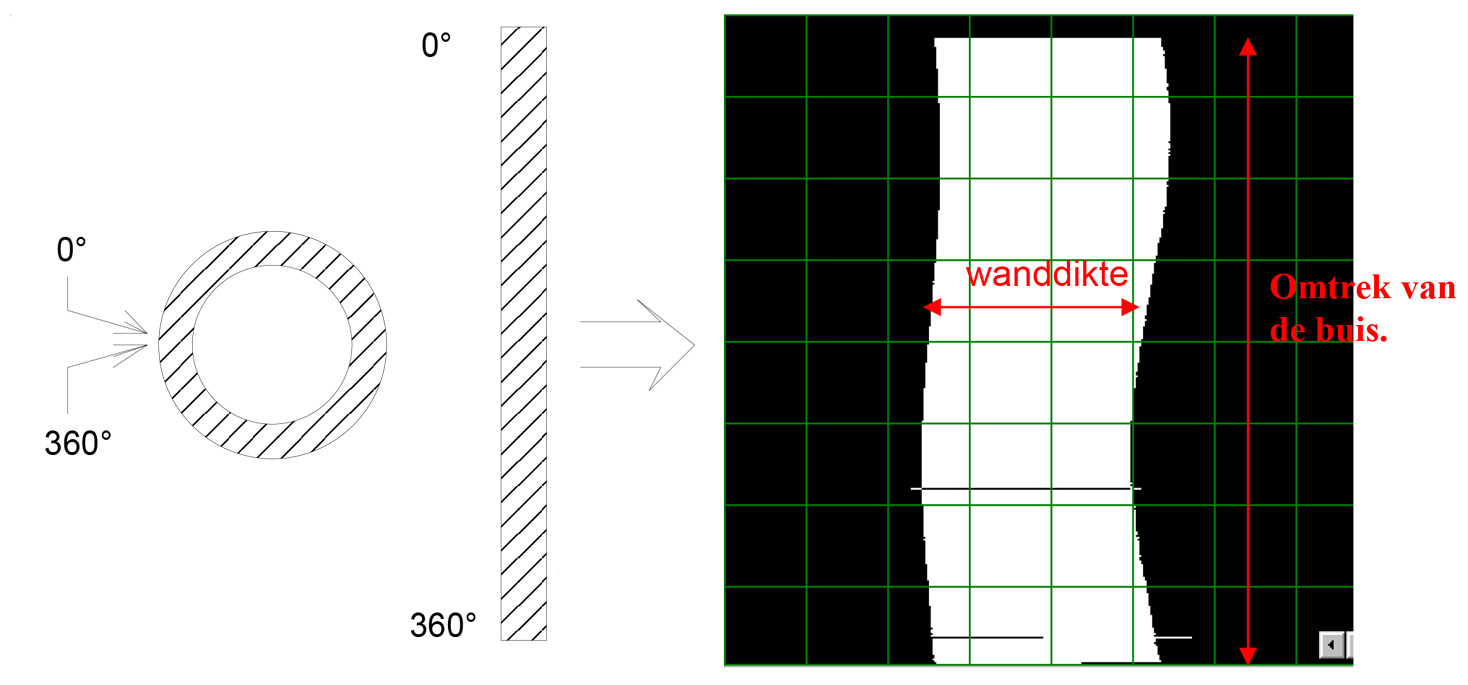
- Comme suggéré ci-dessus, la hauteur de l’image correspond à la circonférence du tube.
- La circonférence d’un tube de 3″ est de 239,3 mm. La hauteur de l’écran sur lequel le signal IRIS est affiché n’est que de 140 mm. Par conséquent, la résolution est compressée par un facteur de 1,7.
- Même si le système IRIS détecte les petites fosses, il est toujours difficile pour l’inspecteur de détecter ces fosses dans la pratique, comme pour les tuyaux de plus petit diamètre.